こんにちは!Team 轟 ホンダ学園 情報処理部門の飯尾です。
車検も無事取得でき、いよいよ10月に入りました。10月といえば体育の日ですよね!私は祝日(休日)が大好きです。
そんな体育の日、どうやら東京オリンピックに合わせて2020年から”スポーツの日”と名称を変えるみたいですね。カタカナ表記であればどうせ外国語約訳する必要が有るし、疑問は有りますが…。
さて!今回はこちらの記事の続きです。どんどんルーフを作っていきましょー!
手順をおさらいするとこんな感じです。
- ルーフ計測
- プラダンでの型作り
- ベニヤ板での型作り
- 発泡スチロール(スタイロフォーム)で型埋め
- パテ盛り
- FRP型作製
- ルーフ作製(FRP積層)
前回は2.プラダンでの型作りまで紹介したので、今回の内容はこちら!
ベニヤ板での型作り
前回までの状態はこちら!
ルーフを作るにあたって手探りの状態で始めたので、少し遠回りになりますが、まずは加工が容易なプラダンで作製しました。
しかし、このプラダンの状態だとFRPを積層するためには強度が足りないのでベニヤ板で同じものを作ります。
まずはプラダンを解体して、それらを基にベニヤ板に転写します。
転写した後はその通りに切り出します。
木枠はこの後組み立てや加工で長く使います。その時にケガをしないよう、きっちりやすり、滑らかにします。
それらを組み立てるとこのように
更に、実車と合わせるとこのようになります。
これで木枠は完成!
スタイロフォームで型埋め
先ほど紹介した木型をベースにFRPを積層するので、まずは隙間を埋めます。
ところで、スタイロフォームと聞いてピンと来る人は少なくないのではないでしょうか?
恥ずかしながら私もこのプロジェクトに関わるまでは知りませんでした。
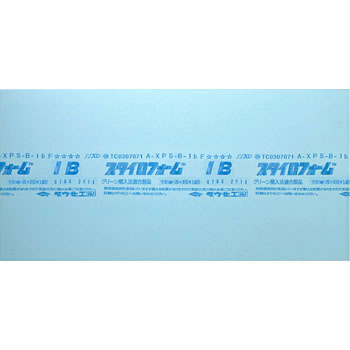
こんな見た目です。
一般名称は「押し出し発泡ポリスチレン」というそうです。
名前の通り、食品宅配サービスや電気機器の梱包などでよく見る発泡スチロールの仲間ですが、発泡スチロールは樹脂の小さい粒がたくさん集まって出来たものに対し、スタイロフォームはその樹脂自体を膨らませている一枚ものの製品なんだそうです。
強度や断熱性等の面でスタイロフォームの方が勝っているそうですが、加工するにあたって一番のメリットは”ボソボソしていない”というところです。
発泡スチロールを割ったり切ってみた経験が有る人はご存知かもしれませんが、なかなか思い通りに加工することが出来ません。
さて、作業としてはまず大体の大きさに切り出します。
カッターなどで切る事も出来ますが、ここでこいつの出番です。
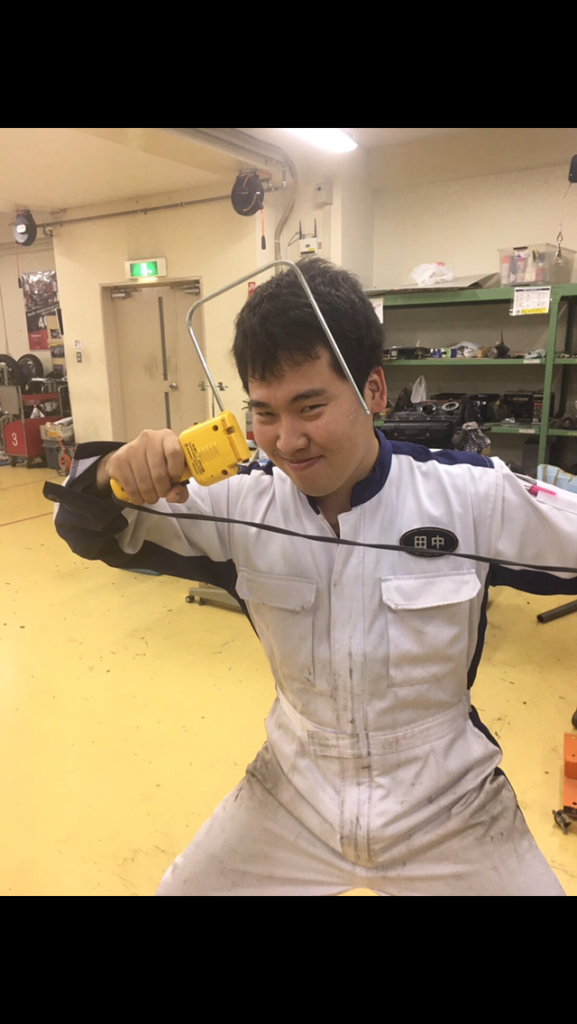
みんな大好きルーフ部門長田中です。
これは電気の力で電熱線を温め、スタイロフォームを溶かすことで切断していく器具です。
今度は切り出したものをスポスポと木枠にはめていきます。
このままでは型として機能しなくなってしまうので、シャコシャコ削ります。
どんどん削ります。
このように滑らかになったら完成です!
削った樹脂が床に落ちたら掃除がめんどくさい床が汚れてしまうので、段ボールで囲いを作っています。
次回予告
木型の完成、いよいよ次はパテ盛りに入る
だがそれはすべての始まりに過ぎなかった
安堵と共にパテを盛る彼らに、事件が迫る
次回、『瞬間、パテ、盛って』
この次も、サービス、サービスゥ!
================
Web部門より。
Web部門の今井です。この記事は10月頃に書かれたものであり、既出の「ルーフ(ハードトップ)を作ってみた!その3」の前編です。
順番が前後し、かなり以前の話になってしまっています事、各位にお詫び申し上げます。
================